碳化硅與硅在汽車(chē)市場(chǎng)大動(dòng)干戈
掃描二維碼
隨時(shí)隨地手機(jī)看文章
在今天的汽車(chē)市場(chǎng),SiC已經(jīng)成為最具活力的技術(shù)之一,設(shè)計(jì)導(dǎo)入機(jī)會(huì)很多,其滲透率正在快速增長(zhǎng)。那么,在EV/HEV系統(tǒng)中,SiC的最大應(yīng)用場(chǎng)景在哪里?BEV被認(rèn)為是汽車(chē)電氣化的終極目標(biāo),因此意味著可持續(xù)的商機(jī)。而且其中的牽引逆變器、蓄電池和電動(dòng)機(jī)是體現(xiàn)不同主機(jī)廠車(chē)輛技術(shù)性能的三個(gè)關(guān)鍵區(qū)別因素。
剛剛過(guò)去的2020年,功率電子行業(yè)的明星莫過(guò)于SiC(碳化硅)開(kāi)始加快了進(jìn)入汽車(chē)行業(yè)的腳步。電動(dòng)汽車(chē)包括三種功率轉(zhuǎn)換器:主逆變器、DC-DC轉(zhuǎn)換器和OBC(車(chē)載充電器),其中主逆變器功率級(jí)別最高,因此也是最需要使用SiC來(lái)提升效率的應(yīng)用,其中功率半導(dǎo)體器件最多,所以是最大的細(xì)分市場(chǎng)。
最大對(duì)手是硅IGBT
今天的SiC正經(jīng)歷硅IGBT技術(shù)所走過(guò)的歷程。1986年,IGBT首次商業(yè)化發(fā)布,之后一發(fā)不可收拾,經(jīng)過(guò)不斷改進(jìn)和發(fā)展,創(chuàng)新器件層出不窮。今天,得益于硅成熟的基礎(chǔ)設(shè)施和工藝,除了性能改進(jìn)外,逐步向12英寸硅晶圓的過(guò)渡,令硅IGBT的成本進(jìn)一步降低,所以SiC等寬禁帶半導(dǎo)體面對(duì)的對(duì)手仍然后勁十足。
不過(guò),SiC MOSFET在更高頻率和溫度下運(yùn)行的特性更勝一籌,是進(jìn)入1200V級(jí)別功率器件的理想選擇,但其高于硅的制造成本,加上IGBT技術(shù)已很成熟,讓最新型的IGBT在市場(chǎng)上仍能立于不敗之地,可以在標(biāo)準(zhǔn)化和廣泛采用方面更進(jìn)一步。
從技術(shù)角度看,SiC MOSFET功率模塊面臨的問(wèn)題和IGBT一樣,模塊中不匹配的CTE(熱膨脹系數(shù))容易使各層相互分離,引發(fā)器件失效。SiC的問(wèn)題更為嚴(yán)重,主要是材料密度引起的熱耗散,因此需要有合適的封裝和系統(tǒng)集成創(chuàng)新方案。
但有一點(diǎn)可以肯定,SiC MOSFET在高溫下導(dǎo)通電阻非常低,結(jié)合其在所有溫度范圍內(nèi)都具有比同類(lèi)硅IGBT更好的開(kāi)關(guān)性能,如果輔以先進(jìn)的創(chuàng)新封裝,既可以簡(jiǎn)化汽車(chē)電力系統(tǒng)的熱設(shè)計(jì),也可以實(shí)現(xiàn)更高效、緊湊和輕量的系統(tǒng)。
電動(dòng)汽車(chē)SiC商用時(shí)代開(kāi)啟
本世紀(jì)初,SiC器件開(kāi)始商業(yè)化應(yīng)用。20年來(lái),它已從國(guó)防軍工等不計(jì)成本的高端市場(chǎng)走進(jìn)尋常市場(chǎng)應(yīng)用。隨著越來(lái)越多的公司開(kāi)發(fā)SiC器件,其發(fā)展勢(shì)頭日益迅猛。在汽車(chē)領(lǐng)域,作為顛覆性技術(shù)的SiC將為電動(dòng)汽車(chē)應(yīng)用帶來(lái)創(chuàng)新和最新的商業(yè)機(jī)會(huì)。
事實(shí)上,SiC的汽車(chē)商用早在2018年即已開(kāi)始。第一個(gè)采用SiC器件封裝解決方案的主機(jī)廠是特斯拉。當(dāng)時(shí),Model 3逆變器搭載了意法半導(dǎo)體(ST)的SiC功率模塊,這是SiC功率模塊在電動(dòng)汽車(chē)中的首次商用。

電動(dòng)汽車(chē)首款商用SiC模塊
ST為特斯拉打造的逆變器由24個(gè)1合1功率模塊組成,模塊封裝在Pin Fin散熱片上。每個(gè)模塊包含兩個(gè)采用片芯連接解決方案的SiC MOSFET,并通過(guò)銅夾直接連接在端子上,以利用銅基板散熱,降低傳導(dǎo)損耗和開(kāi)關(guān)損耗。
同年,英飛凌也推出了第一個(gè)雙面冷卻IGBT模塊FF400R07A01E3,當(dāng)然它還是硅器件;三菱電機(jī)的第7代IGBT J1系列650V大功率汽車(chē)功率模塊也是如此。這些硅基模塊在封裝設(shè)計(jì)和材料解決方案上與ST的SiC MOSFET差別很大。從那以后,研發(fā)SiC MOSFET的頭部半導(dǎo)體公司都加持了SiC,并從市場(chǎng)獲得了很好的回報(bào)。
當(dāng)時(shí),在積極立法的推動(dòng)下,減少二氧化碳排放已成為未來(lái)的主旋律。主機(jī)廠已將汽車(chē)電氣化作為一種非常有效的方式來(lái)減少其車(chē)隊(duì)的二氧化碳排放量,從而避免沉重的經(jīng)濟(jì)處罰。此前很長(zhǎng)一段時(shí)間,標(biāo)準(zhǔn)逆變器功率模塊集成的是硅IGBT,但在電動(dòng)汽車(chē)中,發(fā)動(dòng)機(jī)艙的空間非常有限,很難容納控制電動(dòng)汽車(chē)牽引電機(jī)的功率控制單元(PCU)。因此,PCU必須有更高的功率密度,體積更小。
由于SiC器件可以在更高的結(jié)溫和更高的開(kāi)關(guān)頻率下以更小的芯片尺寸工作,成為了高壓工作條件下硅的有力競(jìng)爭(zhēng)者。然而,高功率密度需要更好的散熱能力,要用新的封裝來(lái)提高器件性能。為實(shí)現(xiàn)這一目標(biāo),制造商們開(kāi)發(fā)了不同的解決方案,例如減少引線(xiàn)鍵合或使用模壓成型(overmolded)結(jié)構(gòu)來(lái)有效地冷卻功率半導(dǎo)體芯片,同時(shí)降低互連電感,提高器件的可靠性。
未來(lái)SiC模塊市場(chǎng)將加速攀升
根據(jù)Yole最近發(fā)布的《2021年電動(dòng)汽車(chē)功率電子產(chǎn)品報(bào)告》預(yù)計(jì),到2026年,電動(dòng)汽車(chē)主逆變器市場(chǎng)將達(dá)195億美元,占整個(gè)電動(dòng)汽車(chē)/混合動(dòng)力汽車(chē)(EV/HEV)轉(zhuǎn)換器市場(chǎng)的67%,復(fù)合年增長(zhǎng)率為25.9%。在功率半導(dǎo)體市場(chǎng),IGBT和SiC模塊之間的技術(shù)角逐的序幕已經(jīng)拉開(kāi),而到2026年后者的價(jià)值將會(huì)翻三番。

xEV半導(dǎo)體功率器件市場(chǎng)預(yù)測(cè)
實(shí)際上,目前SiC模塊的成本仍然是650V IGBT模塊三倍左右,但隨著生產(chǎn)規(guī)模的擴(kuò)大,并逐步采用8英寸晶圓,以及汽車(chē)用戶(hù)應(yīng)用批量的增加,兩者價(jià)格的差距將日漸縮小。
SiC的最大應(yīng)用場(chǎng)景是BEV
在今天的汽車(chē)市場(chǎng),SiC已經(jīng)成為最具活力的技術(shù)之一,設(shè)計(jì)導(dǎo)入機(jī)會(huì)很多,其滲透率正在快速增長(zhǎng)。那么,在EV/HEV系統(tǒng)中,SiC的最大應(yīng)用場(chǎng)景在哪里?Yole認(rèn)為,不同電氣化水平的車(chē)型,包括輕度混合動(dòng)力電動(dòng)汽車(chē)(MHEV)、全混合動(dòng)力電動(dòng)汽車(chē)(HEV)和插電式混合動(dòng)力汽車(chē)(PHEV)、零排放電池電動(dòng)汽車(chē)(BEV)和燃料電池電動(dòng)汽車(chē)(FCEV)對(duì)SiC的需求有所不同。
過(guò)去,人們預(yù)計(jì)向全電動(dòng)汽車(chē)的過(guò)渡速度會(huì)相當(dāng)緩慢和漸進(jìn)。這主要是由于電池成本高,行駛里程短。近幾年,由于電池技術(shù)的快速發(fā)展、制造成本的降低、供應(yīng)鏈的整合等諸多因素,BEV的發(fā)展正在提速。
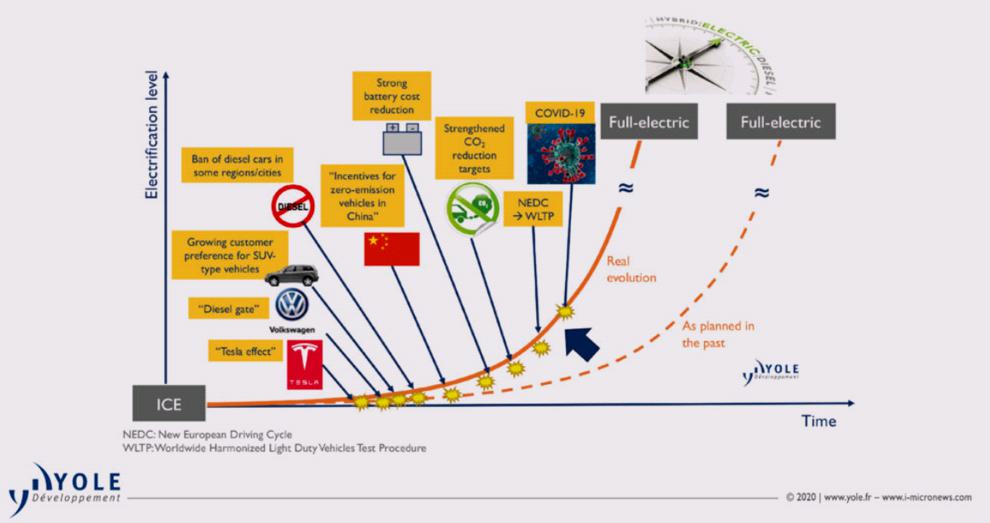
汽車(chē)電氣化發(fā)展進(jìn)程
BEV被認(rèn)為是汽車(chē)電氣化的終極目標(biāo),因此意味著可持續(xù)的商機(jī)。而且其中的牽引逆變器、蓄電池和電動(dòng)機(jī)是體現(xiàn)不同主機(jī)廠車(chē)輛技術(shù)性能的三個(gè)關(guān)鍵區(qū)別因素。特別是逆變器效率的提高可以降低從電池到電機(jī)的能量損耗,延長(zhǎng)行駛里程,直接影響車(chē)輛的性能和用戶(hù)的駕駛體驗(yàn)。
現(xiàn)在,主機(jī)廠在功率模塊的設(shè)計(jì)和制造方面越來(lái)越激進(jìn)。但由于開(kāi)發(fā)高性能、低制造成本的功率模塊封裝對(duì)主機(jī)廠來(lái)說(shuō)有一定難度,一些主機(jī)廠更傾向于直接采用上游廠商提供的SiC MOSFET模塊。
因此,SiC技術(shù)應(yīng)用成功的關(guān)鍵因素之一是供應(yīng)鏈安全。在最初特斯拉Model 3、Model S和Model X相繼采用SiC后,不僅展示了SiC在牽引逆變器中的全部性能優(yōu)勢(shì),也縮小了硅和寬帶隙之間的鴻溝。自那時(shí)起,汽車(chē)用SiC器件的發(fā)展速度不斷加快,主逆變器和車(chē)載充電器設(shè)計(jì)成倍增加,搭載SiC的新車(chē)型也開(kāi)始增多。
2020年,作為特斯拉競(jìng)爭(zhēng)對(duì)手的主機(jī)廠都搭載了全SiC模塊的主逆變器:比亞迪推出了純電動(dòng)車(chē)車(chē)型“漢”,Lucid推出了Lucid Air。韓國(guó)現(xiàn)代、奧迪、大眾、戴姆勒和通用汽車(chē)也都在研發(fā)SiC解決方案。
隨著SiC器件的成功應(yīng)用,為了滿(mǎn)足日益增長(zhǎng)的需求,領(lǐng)先襯底制造商Cree、SiCrystal(ROHM)、II-VI等在晶體生長(zhǎng)方面進(jìn)行了大量投資,而幾乎所有領(lǐng)先的設(shè)備制造商都收購(gòu)或加速了晶圓技術(shù)的內(nèi)部增長(zhǎng)。2019-2020年間,領(lǐng)先的SiC器件制造商ST、英飛凌和安森美半導(dǎo)體(ON Semiconductor)與頭部晶圓和SiC晶體供應(yīng)商Cree|Wolfspeed、SiCrystal和GTAT等簽署了長(zhǎng)期合作協(xié)議。

涉足車(chē)用SiC的上下游廠商
自從800V電池系統(tǒng)電動(dòng)汽車(chē)問(wèn)世以來(lái),1200V SiC越來(lái)越受到人們的關(guān)注。經(jīng)過(guò)幾年的發(fā)展,針對(duì)牽引逆變器應(yīng)用的1200V SiC MOSFET技術(shù)已成為眾多器件制造商的優(yōu)先選擇。下一個(gè)重點(diǎn)是開(kāi)發(fā)合適的封裝,以充分利用SiC MOSFET的附加價(jià)值。
“面向制造的設(shè)計(jì)”是關(guān)鍵
在電動(dòng)汽車(chē)中,發(fā)動(dòng)機(jī)艙的可用空間非常有限,因此,電動(dòng)汽車(chē)中的電動(dòng)傳動(dòng)系要更小,還要有更高的功率密度。這就需要用新的封裝來(lái)提高器件性能。事實(shí)上,在更高的溫度下,標(biāo)準(zhǔn)塑封可能會(huì)在不同層面上出現(xiàn)可靠性問(wèn)題,包括其中的引線(xiàn)鍵合、基板到封裝的連接。此外,為了在競(jìng)爭(zhēng)激烈的市場(chǎng)中保持競(jìng)爭(zhēng)力,功率模塊制造商必須在高可靠性和保持成本效益之間取得平衡。
事實(shí)上,具有最高性能的解決方案并不一定是客戶(hù)需要的,功率模塊材料的選擇和設(shè)計(jì)是影響器件性能的基礎(chǔ),而“面向制造的設(shè)計(jì)”是降低成本的關(guān)鍵。
由于電動(dòng)汽車(chē)仍然是一個(gè)相對(duì)較新的業(yè)務(wù)領(lǐng)域,許多參與者都在通過(guò)高性能來(lái)實(shí)現(xiàn)產(chǎn)品的差異化。這通常是通過(guò)使用專(zhuān)有模塊設(shè)計(jì)來(lái)實(shí)現(xiàn)的,即采用能夠?qū)崿F(xiàn)高性能的封裝解決方案,以保證根據(jù)性能要求將模塊更好地集成到最終系統(tǒng)中。
從應(yīng)用看,在實(shí)際封裝中可以發(fā)現(xiàn)不同的趨勢(shì),包括:轉(zhuǎn)移模塑(transfer molding)結(jié)構(gòu)、塑料外殼、金屬外殼;基板上Pin-Fin散熱器;基板組件集成設(shè)計(jì);單面或雙面冷卻技術(shù);SiN-AMB(氮化硅-活性金屬釬焊)基板;銀燒結(jié)片芯連接、絲網(wǎng)印刷、錫基連接。事實(shí)上,SiC片芯、銀燒結(jié)片芯連接和SiN-AMB陶瓷基板已成為最高性能、最高可靠性的電動(dòng)汽車(chē)牽引逆變器SiC功率模塊的“金三角”。
在封裝方面,模壓雙面冷卻模塊以散熱器封裝取代了塑料外殼,使逆變器更加緊湊和高度模塊化。例如日立2019年為奧迪e-tron和保時(shí)捷Taycan開(kāi)發(fā)的雙面冷卻功率模塊以集成基板為金屬外殼,采用直接水冷型雙面冷卻實(shí)現(xiàn)了逆變器的小型化。

SiC模塊封裝設(shè)計(jì)因車(chē)而異
無(wú)獨(dú)有偶,英飛凌和豐田也開(kāi)發(fā)了雙面冷卻解決方案。其模塊的不同不僅是開(kāi)關(guān)的數(shù)量,而且材料也不一樣,包括引線(xiàn)框架、側(cè)壁(Spacer)和片芯連接材料。
此外,基板對(duì)散熱有很大影響;銅已被廣泛用作引線(xiàn)框架材料,而新型集成散熱片Pin Fin、AMB陶瓷基板正日益受到重視。此外,焊料在提高模塊可靠性方面的作用不可小覷,特別是在更高的溫度下。銀燒結(jié)的使用越來(lái)越普遍,無(wú)論是在片芯下還是在基板下都有使用。
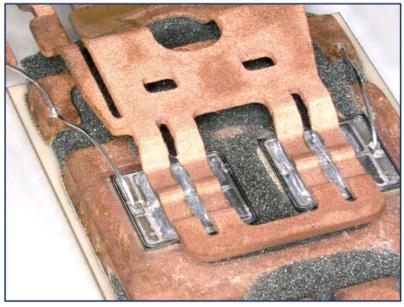
散熱系統(tǒng)需要?jiǎng)?chuàng)新
為了減少連接引起的電感,人們發(fā)現(xiàn)粗線(xiàn)連接已經(jīng)落伍,銅夾或更寬的連接更具優(yōu)勢(shì)。在灌封膠方面,三菱J1系列650V大功率汽車(chē)模塊使用了新的導(dǎo)熱環(huán)氧樹(shù)脂,而不是傳統(tǒng)的硅膠。環(huán)氧樹(shù)脂的散熱性比較好,具有更好的耐高溫特性。
競(jìng)爭(zhēng)將降低SiC成本
我們現(xiàn)在可以自信地說(shuō),SiC將不斷與低成本且成熟的硅直接競(jìng)爭(zhēng),而硅本身就是一個(gè)移動(dòng)的靶子。可以預(yù)期,在最初關(guān)注高性能和高可靠性之后,SiC的開(kāi)發(fā)重點(diǎn)將轉(zhuǎn)向降低成本,以更好地與硅基IGBT功率模塊進(jìn)行競(jìng)爭(zhēng)。
在封裝方面,功率模塊正朝著使用高性能材料和減少層數(shù)、尺寸和接口,同時(shí)保持電氣、熱和機(jī)械特性的方向發(fā)展。未來(lái)將會(huì)有更多的創(chuàng)新設(shè)計(jì)和封裝解決方案出現(xiàn),特別是可以通過(guò)集成節(jié)約成本的解決方案。
鑒于SiC在電動(dòng)汽車(chē)和混合動(dòng)力汽車(chē)逆變器和充電基礎(chǔ)設(shè)施、光伏(PV)逆變器和電源中的應(yīng)用日漸增加,英飛凌、Wolfspeed、ST、ROHM、三菱電機(jī)和許多其他老牌硅公司都提供了SiC組合。
在生態(tài)系統(tǒng)方面,最有力的競(jìng)爭(zhēng)者之一是Wolfspeed。這家垂直整合的SiC公司從襯底材料到SiC器件生產(chǎn)環(huán)環(huán)相扣,為汽車(chē)主機(jī)廠贏得了多項(xiàng)設(shè)計(jì)導(dǎo)入。最近,該公司加大了投資。計(jì)劃于2022年在紐約開(kāi)設(shè)新的制造工廠,進(jìn)一步完善生態(tài)系統(tǒng)。
在這個(gè)令人興奮的市場(chǎng),我們將見(jiàn)證功率電子行業(yè)一個(gè)非凡SiC時(shí)代的開(kāi)啟!